最高性能のセラミックベアリングと最高性能のスチールベアリングの摩擦損失の差はわずか0.03ワットだ。FrictionFactsの実験データで明らかになった事実である。セラミックスピード社のUFOオイルや、MoltenSpeedワックスの抵抗が小さいと知られるようになったのも同社の実験がきっかけだった。
FrictionFactsの目的はただ1つ、「最も抵抗が小さい機材をつきとめる」ただそれだけだ。
「それだけだ」という言葉の裏にはさまざまな意味が込められている。事実とは、ブランドに対する信仰や、個人的な思い入れ、値段が高いから、といった面倒なバイアスから私たちを切り離してくれる。冷静に物事を判断しようとしたとき、感情論や希少性などは性能に影響を与えない。
必要なのは、無機質な実験によって序列がつけられること、ただそれだけである。
「抵抗が大きい」と「抵抗が小さい」だけが定義され、無機質なデータだけが並べばいい。これから記事で紹介していくベアリングの摩擦損失(ワット)の話も同様だ。セラミックベアリングよりも、スチールベアリングのほうが場合によっては優れる、という事実が登場する。
ベアリングに詳しい人にとっては当然の事実である一方で、プロモーションにまんまとやられているサイクリストにとってはウソだと思うかもしれない。そして、データを突き付けられて「しかし、そうは思いたくない」というバイアスと戦っていくことになる。
筆者自身がそうだ。S-WORKS VENGEにはセラミックスピード社のBBを使っているし、ありとあらゆるBBをセラミックに打ち変えたいと今このときも思っている。ただ、FrictionFactsの実験結果を見て「自分自身のバイアス」に向き合う準備をはじめた。どのようなバイアスかと問われれば、「セラミックベアリングに投資してきたから」という事実に対してである。
セラミックベアリングに対する投資はサンクコストになりうる可能性がある。安価なスチールベアリングのほうが高性能とう事実を知り機材変更をすれば、「回収ができなくなった投資費用」として受け止める必要がある。イニシャルコストやランニングコストと同様に、機材決定に影響する重要な要素だ。
今回の記事は、ボトムブラケットのベアリングの摩擦損失に関する実験データを紹介する。そこでわかった事実とは、ベアリングの摩擦損失を決定するものは、材料の「種類と品質(セラミックとスチールなど)」に”必ずしも”依存せず、材料の「設計と品質」に基づいていたことだ。
- ボールの素材(セラミックやスチール)は摩擦抵抗にほとんど影響を与えない。
- シールやグリスは摩擦抵抗におおきく影響を与える。
ボトムブラケットの総摩擦損失に対して、個々の部品を分析する場合、「シール」と「潤滑剤」の摩擦損失はベアリングの総摩擦抵抗に対して支配的であるという事実がある。そして、NTN、NSK、シェフラーといった大手ベアリングメーカーのデータを交えつつ、FrictionFactsの実験結果を合わせながら、セラミックベアリングとスチールベアリングの戦いの行方を追う。
本記事の文字数は17000と多く読了まで30分ほどかかるためブクマするなり、複数回に分けて読むことをおすすめします。
摩擦損失が小さいBB
BBに荷重(5章 実験の詳細を参照)をかけた状態における、摩擦損失が小さいBBは以下のとおり。
ブランド | 損失(W) | BB材質・規格 |
ゴールドレース | 0.29 | セラミック、BB30 |
エンデューロXD-15 | 0.31 | セラミック、標準ねじ |
Cベアロード | 0.31 | セラミック、標準ねじ |
ホークレーシング | 0.32 | スチール、標準ねじ |
ホークレーシング | 0.34 | スチール、BB30 |
セラミックスピード | 0.42 | セラミック、BB30 |
セラミックスピード | 0.45 | セラミック、標準ねじ |
エンデューロセラミックゼロ | 0.45 | セラミック、標準ねじ |
摩擦損失が大きいBBは以下のとおり。
ブランド | 損失(W) | BB材質・規格 |
KCNCテーパーローラー | 2.13 | スチール、標準ねじ |
SRAM Truvativ | 1.64 | スチール、BB30 |
シマノアルテグラ | 1.48 | スチール、標準ねじ |
シマノデュラエース9000 | 1.45 | スチール、標準ねじ |
シマノデュラエース7900 | 1.38 | スチール、標準ねじ |
FrictionFactsが行った実験では、上記の結果が得られている。ホークレーシングのスチールベアリングよりもセラミックスピードのセラミックベアリングのほうが抵抗が大きいという結果だ。「セラミックベアリングだから摩擦抵抗が小さい」わけではない。
本結果が導き出された実験の概要を見ていく。
実験の概要
実験の条件として、ライダーがバイクに乗車している状態を想定しBBに荷重をかけながら摩擦損失の測定を実施した。サイクリストはクランクを介し、BBの垂直方向や横方向に対して荷重をかける。垂直方向(ラジアル)の荷重だけ、軸と同一方向(アキシアル)の荷重だけという「実験室的な」荷重のかけ方は存在しない。
「無負荷状態」や「手で回したときに10分回る」といったたぐいの評価は、「無負荷状態のボトムブラケットの比較」で実施している。さらに、実際の実験ではベアリングにラジアルおよびアキシアル荷重をかけて実験を実施している。
本来ベアリングには負荷(ライダーの体重やペダリングの踏力)がかかった状態で回転することが求められる。負荷がかかった条件下で、摩擦損失がどれほど発生するのかを評価する必要がある。無負荷状態の場合、ボールの変形やBBのベアリング間の距離を考慮はされない。
BBの規格の違いによって、ベアリング間の距離が異なる。この幅の大小がもたらす摩擦損失の違いについても実験内でふれている。今回の実験ではBBの規格の違いに限らず「ラジアル方向とアキシアル方向に対して同一の負荷」を加えている。
無負荷状態の試験でわかることは、ボトムブラケット内のベアリングの摩擦成分(シール、グリス、材質)の違いを明らかにするだけであるため、実環境での性能試験(負荷状態)とは分離して整理する。
基本的なペダリングの仕組みを考えると、ペダルを踏むたびにフレームはラジアル方向と横方向から荷重がかかる。今回の実験では、純粋なラジアル荷重に横荷重を加えテストが実施された。
まず、実験で用いるボトムブラケットの種類、材料、荷重条件について明確に定義する。荷重条件は、およそ50kgの純粋なラジアル荷重(パターン1)と、左右から10kgの横荷重を加えつつ50kgのラジアル荷重を組み合わせた(パターン2)の2通りで構成された。さらに無負荷状態での効率(パターン3)についても分析された。
実験で使用したボトムブラケットのサンプルは、3種類の規格から構成されている。「標準ねじ(スレッド式)」、「プレスフィット30」、「BB30」の3つだ。ベアリングの素材として「スチール」と「セラミック」の2通りがテストされた。
ボトムブラケットの実験サンプルは、それぞれのシェル(BB30、PF30、または標準ねじ)に取り付けたあと、試験装置に配置された。できるだけ現実的な条件に近づけるためにクランクナット(チェーンリングとは反対側のクランクを締め込む部品)の締め具合の荷重量を再現できるよう、外側のクランプを介してボトムブラケットに軽い荷重をかけている。すべてのテストは95 RPMで実行された。
結果
実験の結果は以下の通り。
上のグラフは、負荷がかかった状態での各サンプルの平均摩擦損失を示している。示されている摩擦損失(ワット)は、3つの負荷試験条件の加重平均を示している。ボトムブラケットには、ベアリングモデル、ベアリング材料、およびボトムブラケット規格のラベルを付与している。
加重平均の重み付けとしては、各ボトムブラケットの平均摩擦損失を決定するために、純粋なラジアル測定に80%、ラジアル/左側の測定に10%、ラジアル/右側に10%の測定を組み合わせている。
負荷がかかった状態のボトムブラケットの摩擦損失は、最も低い値(ゴールドレース、セラミックBB30)0.27ワットから最も高い値(KCNCローラーベアリング、スチールST)2.13ワットで、 平均が0.77ワット、中央値は0.63ワットだった。
上記のグラフは、加重平均を含む3つの負荷条件のそれぞれにおいて測定された摩擦損失が分類されている。
- 緑色:純粋なラジアル荷重の測定値
- 黄色:左側と右側のラジアル/アキシアル荷重測定値
- 赤色:加重平均
ボトムブラケットの用途程度では、ラジアル深溝ベアリングとアンギュラコンタクトベアリングのそれぞれで、3つの荷重条件いずれに対しても良好に機能した。どのタイプのベアリングも、特定のタイプの負荷に関して不利な状態に陥ることはなかった。
上のグラフは、「セラミック」と「スチール」の2つの材料に分けて、材料間の効率の違いを分析した結果だ。上記のグラフは、軸受材料の種類ごとの平均摩擦損失を示している。セラミック製ボトムブラケットの平均摩擦損失は0.60ワットで、スチール製ボトムブラケットの平均摩擦損失は1.02ワットだった。
セラミックとスチールの素材の違いに関して細かな説明は割愛する。セラミックベアリングに対するサイクリストの一般的なイメージとして「スチールベアリングよりも摩擦が小さい」という間違った結論を導きがちだ。テストした35種類のボトムブラケットサンプルのうち、多くはハイエンドセラミックで、他のサンプルはローエンドスチールだ。
最高性能のセラミックサンプルと最高性能のスチールサンプルの摩擦損失をそれぞれ比較すると(0.29ワットのゴールドレースと0.32ワットのHawk Racing)、その差は0.03ワットしかない。本測定結果は、特定のスチール製ベアリングボトムブラケットが最高のセラミックベアリングベアリングボトムブラケットと同じくらい効率的に機能することを示している(その差は0.03ワット以内)。
したがって、セラミックベアリングのボトムブラケットは、スチールベアリングのボトムブラケットよりも必ずしも効率的ではないといえる。ベアリングの材質は摩擦損失に対して支配的ではない。ボトムブラケットの効率を決定する要素は、素材自体ではなく使用する素材の設計や構造に基づいている。
「セラミックはスチールよりも摩擦損失が小さい」といった一般的な説明は必ずしも当てはまらない、という結論が導き出せる。
上の図は、同一メーカー内でセラミックとスチールを比較している。セラミックモデルとスチールモデルの両方の摩擦損失を示している。本テストでわかることは、5つのメーカーのうち3社(Enduro、FSA、SRAM)のセラミックベアリングは同社の安価なスチール製品よりも摩擦損失が大きい結果が示されている。
メーカー | セラミックモデル | 損失ワット | スチールモデル | 損失ワット |
FSA | MegaExoセラミック | 1.27 | MegaExo | 1.06 |
SRAM | GXP BlackBox | 0.60 | GXP | 0.53 |
エンデューロ | セラミックハイブリッド | 0.68 | ABEC-3 | 0.64 |
そして、材料そのものだけでなく規格の品質とボトムブラケットの材料の品質も考慮する必要がある。
上記の図は、ねじ式(スレッド)BBとBB30の摩擦損失の比較だ。すべてセラミックハイブリッドベアリングで統一されており、BBの規格が異なっている。同一材料で作られた同一メーカーのボトムブラケットモデルの16サンプル(8ペア)で構成されている。摩擦損失の中央値は、BB30が0.56ワットで標準ねじが0.49ワットだ。
摩擦損失は、規格に依存せず、製造業者、品質、およびボトムブラケットの設計に依存している。ベアリングレース中心点から、ベアリングレース中心点(有効幅)は、BB30およびPF30標準のものよりもスレッド式ボトムブラケットのほうが大きい。ボトムブラケットの幅を広げると、BBに対して同じ踏力が与えられたとしてもベアリングのラジアル荷重が(スレッド式のほうが)効果的に減少することがわかっている。
「ボトムブラケットの幅」と「ラジアル荷重」の関係をふまえ、本実験と結果における注意点を補足しておく。すべてのボトムブラケットサンプルは、スレッド式やBB30の規格に関係なく、同様の負荷条件でテストされた。
すなわち、「同じ荷重条件下」でボトムブラケット幅が異なる対象を分析していることになる。ボトムブラケットの幅の影響を考慮するとより幅広いスレッド式BB摩擦損失は、同等素材を用いたBB30もしくはPF30よりも約5~10%低くなると推定されている。
上の図は、無負荷状態のボトムブラケットの比較データだ。荷重を取り除いて試験を実施した。単純にシールと潤滑剤が総摩擦損失にどのような影響を及ぼすのかを測定している。本試験項目の実施理由は、各ボトムブラケット内の摩擦損失の成分を把握するためである。
自転車でベアリングを使用することを考えた場合、ここまでの実験のようにベアリングには負荷をかけた状態で摩擦損失を測定することが望ましい。無負荷状態の試験でわかることは、各ボトムブラケット内のベアリングの摩擦成分が明らかになるだけである。
したがって、実際に走る際に発生するベアリング内の摩擦損失の考え方とは別の話題であり、切り離して考える必要がある。
ボトムブラケットによって生じる摩擦の大部分は、シールが60%とグリスが28%という内訳だ。たった2つの要素が摩擦損失の90%近くを支配している。ベアリングの摩擦の詳細な内訳(シェフラー(FAG / INA)社:ベアリングを構成する要素の摩擦抵抗割合)は以下のとおり。
- シール:60%
- グリス:28%
- リテーナー抵抗:7%
- ボール変形:3%
- レース変形:2%
先程の各ブランドの摩擦損失の話に戻る。無負荷時の平均摩擦は0.40ワット、中央値は0.32ワットだ。無負荷時の摩擦の主な要因としては、シールと潤滑剤(粘性抵抗)によって発生する。たとえば、平均無負荷摩擦(0.40ワット)と平均負荷摩擦(0.77ワット)を比較すると、実際のボールとレースの摩擦(48%)よりも、摩擦全体の大部分が潤滑剤とシールによって生成されていることがわかる(52%)。
[合計負荷摩擦] = [無負荷摩擦(シールおよび潤滑剤が寄与する)] + [負荷摩擦(ボールとレースの相互作用が寄与する)]
この単純な計算は、シールと潤滑剤によって生じる摩擦損失が負荷に「完全」に依存するのではなく、ボールとレースの相互作用によって生じる摩擦損失が負荷に大きく依存するという前提で実施された。理論的に言えば、無負荷のボトムブラケットの摩擦を測定し、全負荷摩擦からそれらを差し引けばよい。結果で得られる値は、負荷下でのボールとレースの相互作用によって生じる摩擦を導き出す。
現実的には、この摩擦損失を分離する方法は理想的ではなく絶対的なものでもない。それでも、それぞれの摩擦を生み出す成分がどのように寄与するのかという一般的な指標を導き出している。
この無負荷の実験では、ボトムブラケットの効率だけを評価している。寿命や耐久性に影響を及ぼす可能性のある、シールや潤滑剤の設計といった重要な機能は考慮されていない。粘度の高いグリスを使用すると寿命が長くなり、粘性抵抗が大きくなる。逆に、粘度の低いオイルは粘性抵抗を最小限に抑えるが、ベアリングの寿命を延ばすためには、メンテナンスを頻繁に行う必要がある。
ボトムブラケットの設計者は、製品の使用目的に基づいた(ロード、シクロクロス、マウンテンバイクといった)要素からどのようにベアリングを保護するか、そして回転の効率のためにシール抵抗を最小化するという相反するバランスを達成することが求められている。
ボトムブラケットのパフォーマンスを最大にするためのアプローチとは、耐久性を備えつつも摩擦損失が小さく効率的なボトムブラケット備えるということになる。
実験結果で最も摩擦損失が小さいGold Race BB30ボトムブラケットは、最大限の効率を高めるための設計アプローチをとっている。シールの内径が実際のベアリング内径よりも小さく設計されている。このすきま(そして非接触シールで摩擦が小さい)とグリスではなくオイルの使用をしていることが、ゴールドレースが最小の無負荷摩擦損失を叩き出した理由だ。
ただし、このような設計ではマッドコンディションや野外での使用を考慮すると適切とは言いにくい。ベアリングの回転を悪くしてしまう汚染物質がベアリングに入りやすくなる。そして、実際にゴールドレースの製造元の推奨は、「トラックおよびクリーンロードレースの使用のみ」としている。
シールと潤滑剤に関して別の効果を示した例は、C-Bear製品で見ることができる。製造元によれば、ロードボトムブラケットとMTBボトムブラケットそれぞれで使用している内部ベアリングは同じだ。ただし、MTBバージョンには、より堅牢なシールとより多くのグリスが組み込まれている。そのため、過酷な条件で使用してもベアリングの寿命と耐久性の向上が期待できる。
しかし、ROADバージョンと比べてMTBバージョンの摩擦損失は+0.54ワット大きくなる。
シール、潤滑剤、およびボールとレースそれぞれが作用しあい、ボトムブラケットの摩擦損失に影響を及ぼす。すべてのサンプルの平均を見ると、「ボールとレース」よりも「シールと潤滑剤」のほうがより摩擦への寄与が大きくなる。
以上のことから、ベアリングに使用されているシールの設計や工場出荷時の潤滑剤は、使用目的、耐久性、寿命、性能に違いを及ぼす。私たちがボトムブラケットを選択するとき、バイクの使用用途にマッチするようにメンテナンス性、構造を理解し考慮することが重要といえる。
なお、実際に「ベアリング」という部品を使用する際は、シールと潤滑剤を除去することは推奨しない。
実験で使用したベアリングの材料
実験で使用したベアリングの材料は以下のとおり。
- スチール
- セラミック
実験で使用した「セラミック」ベアリングを正確に表現すると、実際は「セラミック」「ハイブリッドベアリング」だ。セラミックハイブリッドベアリングは、「セラミックボールベアリング」と「スチールまたはスチール合金のレース」で構成されている。
本実験において「セラミック」と表現される場合は、フルセラミック構成ではなく、セラミックハイブリッド構成を指している。
実験の詳細
それぞれのボトムブラケットには1時間の慣らし運転が実施された。この1時間という時間の目的としては、ベアリングの潤滑剤とシールを慣らすことにある。荷重条件1として、およそ50kgの純粋なラジアル荷重を加えた。慣らし期間のあと、右側に10kgの横荷重を加えた(慣らし期間からボトムブラケットにすでに適用されているラジアル50kgに加えて)。3分後に摩擦損失の測定と記録を開始し、荷重条件2とした。
次に、右側から10kgの横荷重を取り除き、同様の荷重を左側にも加えた(荷重条件3)。3分後に2回目の測定値を記録した。これらの荷重条件は独立して「右横」および「左横」の測定値として計測した。試験装置で得られたデータの平均化は15秒に設定した。つまり、すべての測定値は15秒ごとの枠にまとめられたデータの平均で表されている。
左横方向の測定値が記録されたあと、横方向の荷重が取り除き、純粋なラジアル荷重50kgだけを残した。3分後に測定と記録を開始した。本測定は「純粋なラジアル荷重」の測定を行っている。その後、ラジアル荷重を取り除き、縦横方向共に荷重がかからない状態の「無負荷」で測定を実施した(荷重条件4)。
4つの負荷条件すべてで、実験開始前に試験装置のキャリブレーションを実施し、試験装置自体のベアリング摩擦損失も考慮した。これらの試験装置の摩擦損失は、ベアリング摩擦損失の生データから削除した。したがって、実験レポートに表示される結果データは、テスト中のボトムブラケットサンプルの「摩擦損失だけ」を表している。
負荷の定義
ボトムブラケットのベアリングは、一般的なライディング中に発生するさまざまな負荷にさらされる可能性がある。ベアリングへの荷重負荷は、簡単なペダリングの場合であればわずか数キログラム程度だ。ところが、ライダーの全体重がペダルにかかる場合、180kgを超える負荷がBBに加わる場合がある。
本実験で適用した荷重(純粋なラジアル荷重条件)はおよそ50kgだ。この負荷は、ライダーが250ワットを定常状態でライディングする際にボトムブラケットが受けるおおよその平均負荷をシミュレートしている。この計算の前提条件は次のとおり。
- 出力:250W
- クランク長:175mm
- フロントチェーンリング:53T
- ケイデンス:95RPM
計算は、ペダルの荷重、ペダリングのダウンストローク中のピーク荷重、張力のかかったチェーンによる反力も含まれている。駆動側(チェーンリング側)と非駆動側のベアリングは、ペダルストロークの任意のポイントで異なる負荷を受ける。駆動側(チェーンリング側)のベアリングは、チェーンの反力により、非駆動側のベアリングよりも平均荷重が高くなる。
試験装置
ボトムブラケットの摩擦抵抗を測定する試験装置の測定精度は±0.01ワットだ。
試験装置は比較的単純な設計を使用した。設計内容としては、シャフトを支えるセラミック製の固定ベアリングで構成される。ベアリングに負荷をかけ、シャフトが回転するとシステムの総摩擦が測定される。測定するデータには、ボトムブラケットのベアリングの摩擦損失と、試験装置のベアリングの摩擦損失が含まれている。
試験装置で発生したベアリング摩擦損失は、実際に測定したデータから除外される。結果はテスト対象のボトムブラケットの摩擦損失値だけが出力される。
ボトムブラケットが取り付けられたシェルは、業界標準のBB30、プレスフィット30(PF30)、および標準ねじ付き(スレッド式)シェルを用いた。これらのシェルは、フレームの製造にフレームメーカーが使用するものと同じボトムブラケットシェルであり、フレームコンポーネントのサプライヤから調達している。
試験装置のメカニズムは、シェルの上部に幅広のナイロンストラップを巻きつけてシェルに荷重をかけた。シェル全体に均等に荷重をかけ、左右のベアリングにも均等に荷重を加えた。ボトムブラケットの内径(ID)と一致する外径(OD)のシャフトが、ボトムブラケットに挿入され、クランクのスピンドルを模擬し機能するようにした。
シャフト、ボトムブラケットは、2つのセラミック製ベアリングで支えている。クランプを使用して、シャフトに対してボトムブラケットを固定し、ボトムブラケットに軽い予荷重を与えた。これらのクランプの使用目的は、横方向の荷重条件でシャフトとボトムブラケットが水平方向に滑らないように使用している。
BBのシェル、荷重するためのストラップは固定されている。当然の話だが、シャフトがシェル内で95 RPMで回転してもシェルは静止状態になるように設計している。駆動モーターとシャフトの間に配置された回転トルクセンサーは、ボトムブラケットの2つのベアリングと試験装置側の2つのベアリングによって生じる合計摩擦を(トルクとして)測定する。
一貫した精度を維持するために、テスト全体を通して試験装置には同一のベアリングを使用した。 異なるボトムブラケットの内径規格に適合するには異なるシャフト外形が必要であったため、異なるサイズのシャフトごとにアダプターを製造している。
横方向、縦方向それぞれにおける試験装置のベアリングの摩擦損失は、事前テストキャリブレーションで得られた量を採用している。測定された総摩擦損失から試験装置のベアリング摩擦損失を差し引き、テスト中のボトムブラケットの摩擦損失とした。
第2の実験と分析
第1の実験では、FrictionFactsの実験結果を紹介した。第2の実験では、宇宙工学出身のエンジニアが実施した実験だ。FrictionFactsの実験と同じく、セラミックベアリングとスチールベアリングの比較を実施している。実験の導入ではベアリングの基本構造やNTN、NSK、シェフラーのベアリング摩擦損失のデータを解説する。
ベアリング内部構造
セラミックベアリングは主に、セラミックボールとスチール製の内輪部分と外輪部分から構成された「ハイブリッドセラミックベアリング」だ。セラミックボールは多くの場合、窒化ケイ素または同等の素材で製造されている。
スチールベアリングは硬化スチールで製造され、ベアリングの内外レースも同じくスチールだ。内部設計も多くの場合、接地点、内側と外側の寸法、およびスチールボールとセラミックボールのベアリング間の距離も同じであるため、それぞれのベアリングが交換可能である(スチールボールをセラミックボールに入れ替えるチューニングをしばしば見かける)。
参照資料:NTN 軸受内部すきまと予圧
両者の大きな違いは、ベアリングのクリアランス(軸受内部すきま)だ。 セラミックベアリングはC3のクリアランスの場合が多い一方で、スチールは通常CNのクリアランスを備えている。軸受すきまは、内輪、外輪、およびボールの間の小さなすきまだ。内部すきまの大小は、寿命、振動、騒音、発熱など軸受の性能に大きく影響を与える。
ベアリング構造のもう1つの違いは、保持器(以下:リテーナー)のタイプだ。リテーナーは、ベアリングの周囲全体に対して、ボールの間隔を均等に維持するために使用する。スチールベアリング(日本のメーカーであればNSKやNTN製)では、リテーナーはプレスされた金属片で作られる。比較的コストのかかる工法である一方で、低速での摩擦特性と剛性は向上するメリットが有る。
参照資料:軸受材料 13.2保持器材料(NTN)
これら普及しているリテーナー構造とは異なる工法として、ゴムリテーナーがある。このリテーナーはボールがカチッとリテーナーにはまってボールの間隔を保持する。デメリットとしては高い負荷がかかると、リテーナーからボールが飛び出たり、もしくは変形し摩擦抵抗が大きくなってしまう。セラミックベアリングの場合は、ほとんどの場合コンポジットやゴム製のリテーナーを使用している。
しかし、Campagnoloの「CULTベアリング」はベアリングボールがセラミック製で、カップとリテーナーに特殊加工を施し、セラミックボールの硬さに負けない硬度に仕上げられている(とされている)。そのため、滑らかな回転とグリスが無くとも最小限に摩耗が抑えられ、高い耐久性をが期待できる(とされている)。自転車業界において、「高価」であることを除いては死角の見当たらないベアリングシステムである(とされている)。
CULT(セラミック・アルティメット・レベル・テクノロジー)の開発はCampagnoloではなく、シェフラー・グループ(ドイツ:ベアリング世界2位)のFAG社が開発している。ベアリングのレースには、クロニテクトスチールが使用されている独自の技術だ。この特殊なスチールは最高レベルの耐腐食性を備え、潤滑のためのグリスを塗布する必要はほとんどない。
ベアリングシール
一般的なベアリングのシールタイプは4つある。オープン、金属シールド、非接触シール、接触シールだ。自転車用途で使用するシールは、非接触または接触するシールが採用されている。シールを使用する理由としては、ほこりやゴミの侵入によってベアリング内が汚染されるリスクを減らすためだ。
理論上は、非接触シールとオープンは同じ摩擦レベルを持つはずだ。しかし、実際はそうではない。理由の1つとして、シールは潤滑剤が外に逃げないように中に閉じ込める役割を持っている。本役割は、摩擦損失として扱う。完全に接触するシールは、内側レースと外側レースの両方に接触してシールを維持し、こちらも摩擦損失になる。
重要な密封という役割ながら、ベアリングの総摩擦損失に占める割合としては大きい。手で回転するとその摩擦を感じることができる。60年代に発明されて以降、基本的なベアリングシール技術は変わらず、劇的に変化していない。
ベアリング生産
ベアリングの大量生産は、ほぼ完全に自動化されたプロセスで行われる。ベアリングの大量生産は日本人によって開発された。ベアリング界のビッグ4(SKF、NTN、NSK、およびFAG)は、人間の介入をほとんど必要とせずに毎秒数千個のベアリングを生成する能力を備えている。ベアリングは通常、原材料から箱入りの完成品まで1つの工場で製造される。そして、これらのベアリングのほとんどはスチールベアリングだ。
対照的なのが、小さなセラミックサプライヤだ。セラミックスピードが有名で、Enduro、KOGELといったブランドがよく知られている。これらのブランドは、人間の介入する部分がはるかに多く、多くの場合、ハンドメイドでベアリングを組み立てているサプライヤもある。これら中小企業には、製造プロセス全体を現場で完結する能力がない場合が多い。
通常、ベアリングや複数の部品を第3者の製造業者に下請けを出し、最終的な組み立ても自社内で完了していないブランドもある。セラミックベアリングの一部のサプライヤは、ハイブリッドキットを購入し、ベアリングの側面に独自のブランド名をレーザーエッチングし終わり、というブランドもある。レーザーエッチングがしてあると、高品質でオリジナルベアリングであるかのように装うことができる。
これらのベアリングはアジア(多くは中国)から非常に低コスト(5ドル程度)で仕入れられ、その後、米国、ヨーロッパ、日本の富裕層に原価の10倍、さらには20倍で販売される。これらのメーカーは、NTNやNSKのように詳細な技術データを公開していない(むしろできない)。そして、このようなメーカーは簡単に見つけることができ、判別することができる。
NTN:転がり軸総合カタログ検索:https://www.ntn.co.jp/japan/products/catalog/search.php?categoryId=140&searchWords=
ベアリング摩擦
大手のメーカーには、エンドユーザーの技術的なアドバイスに回答するエンジニアリング部門が設けられている。SKF、NTN、NSK、シェフラー(FAG / INA)は、ベアリングの部品(シール、グリス、転がり抵抗)別の摩擦損失の割合を示す資料をエンドユーザー向けに開示してくれる(下図参照)。
ベアリングの各コンポーネントに関連する摩擦の割合はわずかに異なるが、全体的な値と順序は基本的に同じだ。ベアリングの総摩擦抵抗のうち、ベアリングシールが最大の摩擦損失である。潤滑剤がそれに続く抵抗であり、転がりの摩擦損失は非常に小さいことがわかる。
さらにシェフラー(FAG / INA)は、もう1歩踏み込んだベアリングの構成要素別の内訳も示している。シェフラーのデータが貴重かつ重要である理由として、スチールからセラミックベアリングに変更した場合の有効性と事実を把握するために役立つ。素材をスチールからセラミックに変更したとしても、摩擦抵抗を改善できる割合は最大3%程度しか期待できない。
実際には、転がりの摩擦をなくすことはできないため、3%のうち10%、すなわち0.3%ほどしか摩擦抵抗の削減を見込めない。セラミックベアリングは、ほとんどの場合リテーナー内にスナップがあるため、リテーナーの摩擦に注意する必要がある。これらは、金属リテーナーよりも摩擦が大きいことが一貫して示されている。
したがって、セラミックベアリングは転がり摩擦を減らすことが可能である(3%)が、リテーナーの摩擦は必然的に増加する(7%)。 最終結果としてセラミックベアリングを使用したからと言って摩擦抵抗が小さくなるとは限らない。むしろ、条件しだいではスチールベアリングのほうが摩擦が小さくなる可能性がある。
これらの事実を実際に確認するために、グリスとシールの効果を試す実験を行った。Enduro製のセラミックベアリングとNTN LLB(非接触)スチールベアリングの2つのベアリングを、分解しさまざまな条件の違いで摩擦損失を測定した。下のグラフは右に行くに従い異なるプロセスを示している。
ベアリングは3つの異なる状態に変更しながら測定を実施した。はじめは箱から出したあと、すぐに使用する。2番目はグリスの除去を行いオイルを注油した。3番目はグリスの除去、シールの除去、そしてオイルの交換を実施した。
箱から出した状態において、Enduroベアリングの電力損失はわずかに低くなる。グリスが除去されると、両方のベアリングの電力損失はほぼ等しくなる。 シールを取り外したあと、NTNベアリングの摩擦が優位になる。これは、NTN、NSK、SKF、およびシェフラーが提供するデータと相関関係にある。
ベアリングの摩擦と寿命
ベアリングの試験でしばしば無視されがちなのは、ベアリングが摩耗したときにどのような摩擦損失の変化があるかだ。下のグラフは、2つのスチールベアリング(SKFおよびNTN)とセラミックベアリング(Enduro)の比較を示している。使用が少ない場合は、エンデューロベアリングの摩擦は低かった。しかし、約600kmの使用でセラミックベアリングはスチールレース(比較的柔らかい)の表面を摩耗させた。
結果、ベアリングの摩擦抵抗は劇的に増加し始めた。一定期間の走行後、スチールベアリングよりも摩擦抵抗が高くなる傾向にある。ハイブリッドセラミックベアリングは、アスファルトの道路で機関車を走らすようなものだ。材質と材質の硬度の違いにより、ベアリングの道路(レース)が損傷する。
総摩擦損失
上のグラフは、異なるベアリングブランドとそのシールタイプ間で1000kmにわたってどれだけの電力を節約できるかを示している。NTN、NSK、SKFがこのチャートを支配している。これは、主に効率的なシールと金属ケージによるものだ。赤の棒で示されたセラミックベアリングはそれほど効率的ではない。
評価の範囲が10,000 kmに拡張された場合、セラミックベアリングはレースが摩耗して摩擦が増加し、パフォーマンスが大幅に低下るという結果が得られている。
まとめ:セラミックとスチールどちらを使うか
「セラミックとスチールどちらを使うか」
セラミックベアリングとスチールベアリングに関する長旅を終えた読者は、問いに対しる明確な答えをこれから出す準備ができているだろうか。ここまででさまざまな実験を追いかけてきたが、データが示した真実は、「セラミック=抵抗が小さい」や「スチール=抵抗が大きい」という長年サイクリストが描いてきた幻想や、思い込み、プロモーションの刷り込みを取り払うには十分な結果だった。
「40kmのTTで10秒短縮する」や「1分間も回り続けるクランク」は決して、セラミックという材質で作られたベアリングだけが摩擦抵抗に影響を与えたわけではないのだ。クランクがいくら勢いよく回転したとしても、「無負荷状態のベアリング」であるということを忘れてはならない。
摩擦損失は、材質の要素よりも、シール、グリス、クリアランスといった要素に支配される。ただ、ベアリングを仕入れて売りつけようとした場合、ベアリングに詳しくない人にとってはわかりやすい違いのほうが魅力的に思わせることができ、財布の紐をゆるませることができる。
「軸受内部すきまが・・・」「高荷重状態での回転が・・・」というメリットをたとえ語られたとしても、なかなか買おうとは思わない。それよりも「10分回り続けます」というキャッチーなプロモーション(ただし無負荷状態である)のほうがよほど効果的だ。しかし、サイクリストたちの購入意欲を向上するには有効である一方で、性能の向上に必ずしも結びつくわけではないことを理解しておかねばならない。
「数百円のベアリングがセラミックスピードをしのぐ」
プロがこぞって使い、プロのハイエンドバイクに採用(もちろんプロモーション費用が上乗せ)されているセラミックスピード社のセラミックベアリングよりも、NTNやNSKといった日本ブランドの非接触(LLB、VV)スチールベアリングのほうが抵抗が小さいという実験結果が公表されたわけだ。にわかに信じがたい事実である一方で、日本のベアリングメーカーの底力を再発見できた。
ここまでの結果を通じて、1つだけベアリングを選択してみよう。あなたは何を選ぶだろうか。私はTREKのBB90用にNTNのベアリング(LLU)を購入した。わずか600円である。「ベアリング」に対する思いはそれぞれだ。プロが使っているからでも良いし、ブランドへの忠誠もある。いわば宗教に近いベアリングの世界だが、そこには実験で明らかになった事実が存在していた。
今回、セラミックベアリングを販売するブランドにとっては非常に厄介な実験データが並んだ。一方でTOJにスポンサーを行うNTNはさらに一歩輪界に踏み込んで違った角度のプロモーション(ハブやBBのベアリングを同社の製品に打ち替える場合の互換表をTOJで配布など)を実施したほうがよほどプロモーションに対するリターンは大きいだろう。
TOJ NEWS 更新「大阪市西区に本社を置く世界的なベアリングメーカー NTN株式会社 が2020年も ツアー・オブ・ジャパン の冠協賛社に決定!」 https://t.co/rR0ZoEU6PV #tojhp pic.twitter.com/qhtZbPqjGu
— Tour of Japan (@tourofjapan) January 17, 2020
私はシクロクロスバイクのBBをシーズンごとに交換している。純正部品のコストは2つで4000円だ。しかし、これからはNTNのベアリングセットで1200円だ。高品質な日本製ベアリングである。なお、自転車用であれば実験で登場するLLBよりもLLUがいい。
今回のベアリングに関する実験を通じて思うことがある。世の中は不条理な慣例が蔓延し、無知な消費者をターゲットにして利益を巻き上げることに躍起になっているショップやメーカーも中にはある。NTNベアリングのように高品質で性能が高く、安価な製品が存在していたとしても、ショップが提案することはほとんど無いだろう。
これまで、BBやハブベアリングの打ち替えでNTNやNSKのベアリングを取り寄せて取り付けてくれたショップがあったのなら、長いおつきあいを考えたほうがいい。そして、その逆は言わずもがなである。もしも、ショップさんでお客さんのベアリング規格を調べてNTNといった製品に打ち替えてくれる所があれば、記事のシェアやFacebookページのコメント欄で宣伝していただいても構わない。
「純正品ではないから」という決まり文句を言いつつも、その海外ブランドの「純正品」にはMade in Japanの文字が誇らしげに刻印されている可能性がある。NTNのようなベアリングが代替品として使用できるという事実や、存在を知らなければ手にとることも、使用することもできないのだから。
今回の記事はセラミックベアリングとスチールベアリングの摩擦損失にフォーカスした。しかし、セラミックベアリングがスチールベアリングよりも優れているというのは条件しだいだ。ボールの材質は総摩擦損失に対して支配的ではない。これらの結果が、ベアリングの選択に長年悩んできたサイクリストたちの1つの判断材料になれば幸いである。
秀和システム
売り上げランキング: 350,805
なお、実験を行ったFrictionFactsはセラミックベアリングを完全に否定しているわけではなく、品質、価格、性能、シール選択(ROAD・CROSS)を選べるKOGELもしくはHSC ceramicsを推奨している。
当ブログでは、TREK BB90ベアリング(スチール)であればモノタロウで615円のNTN 深溝玉軸受 6800番台 LLU (両側接触ゴムシール形) をおすすめしている。59種類のベアリングからお好みの1つを選んでほしい。きっとあなたに合うベアリングが見つかるはずだ。セラミックベアリングであれば、FrictionFactsと同じくKOGELを使用している。
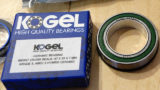