記事の要点。
- ベアリングの効率は設計と素材の質に基づいている。素材の種類(セラミックやスチールなど)で決定しない。
- ベアリングに生じる摩擦抵抗のうち60%がシール、28%がグリースと潤滑油、7%がレースやリテーナー、3%がボールの割合である。
- 総摩擦損失は「シールと潤滑油ロス > ベアリングロス(ボールとレースの相互作用摩擦)」の関係にある。
- 最高性能のセラミックと最高性能のスチールの摩擦損失を比較するとその差は0.03ワットしかない
- プロモーションで行われる無負荷、無荷重時の回転はシールと潤滑油の抵抗が支配的である。ボールやセラミック素材などの性能を十分に示すものではない。
セラミックベアリングは本当に抵抗が小さく効果があるのか。いまだ妄信的に「セラミックは摩擦抵抗が小さく鉄球よりも性能が高い」という、洗脳にも似た通説を無機質なデータと数字が解き明かしていく。本記事を読み進めれば、無負荷のベアリングフリースピンをありがたがるユーザーや、売るための子供だましのプロモーション、見かけだけのトリックに正しい判断を下せるようになる。
第三者機関であるフリクションファクトが検証した。実際の条件を考慮した縦加重、横加重を加えた摩擦試験から、プロモーション目的で蔓延する”無意味な無加重”の摩擦抵抗測定も行われた。
実験で判明したことは、「セラミックはスチールより摩擦抵抗が小さい」という一般的な表現は真実ではなかった。
最高性能のセラミックベアリングと最高性能のスチール(鉄球)ベアリングの摩擦損失の差は、わずか0.03ワットだった。予想に反して、3つのメーカーのスチール製ベアリングは、セラミック製ベアリングよりも摩擦抵抗が小さかった。
ベアリングの効率は、設計と素材の質に基づいている。必ずしも素材の種類(セラミックやスチールなど)によって決まるわけではない。
総摩擦損失に寄与する個々の部品を分析すると、「シール」と「潤滑油」による摩擦損失は、ベアリング自体による摩擦損失(ボールとレースの相互作用摩擦)よりも大きい。つまり、摩擦損失は以下の関係が成り立つことがわかった。
ベアリング効率の調査
さまざまなメーカーと規格の35個のベアリングについて、さまざまな負荷条件下での効率(摩擦損失)を分析した。
手順概要
サイクリストが地面に対して純粋に垂直な姿勢でいることはめったにない。 基本的なペダリングのメカニズムでは、ペダルを踏むたびに自転車は垂直から外れた姿勢になる。激しい加速や登り坂では、より垂直から外れた位置が拡大する。
垂直から外れたどのような方向でも、BBに横方向荷重の成分が生じる。BBは、純粋な縦方向の垂直方向荷重に加えて、横荷重もテストされた。
荷重方法、BBタイプ、素材:
荷重条件は、52キログラムの純粋な垂直方向荷重と、52キログラムの垂直方向荷重と9キログラムの横荷重の組み合わせで、左右にそれぞれ負荷をかけた。 BBは、無負荷状態での効率についても分析した。
サンプルは、標準ネジ式、PF30、BB30の3種類のBBで構成した。スチール製とセラミック製ハイブリッド・サンプルの両方をテストした。 詳細については後述する。
荷重条件は以下の通り。
- 52キログラム 垂直方向のみ
- 52キログラム 垂直方向 & 9キログラム・横方向(右)
- 52キログラム 垂直方向 & 9キログラム・横方向(左)
- 無負荷
BB・タイプは以下の通り。
- Standard Threaded (ST):ねじ切り
- Press Fit 30 (PF)
- BB30
BB・ベアリング材質は以下の通り。
- スチール(鉄)
- セラミック
テストで使用したセラミックベアリングは、実際にはセラミックハイブリッド設計である。セラミックハイブリッドベアリングは通常、セラミックボールベアリングとスチールまたはスチール合金レースを使用している。
本レポートにおける「セラミック」という用語の使用は、フルセラミック設計ではない。セラミックハイブリッド設計を表している。
平均摩擦の決定:
各BBの平均摩擦損失を求めるため、純粋な半径方向の測定値の80%、半径方向/左横方向の測定値の10%、半径方向/右横方向の測定値の10%を合計した。 この計算により、加重平均が得られる。
結論:
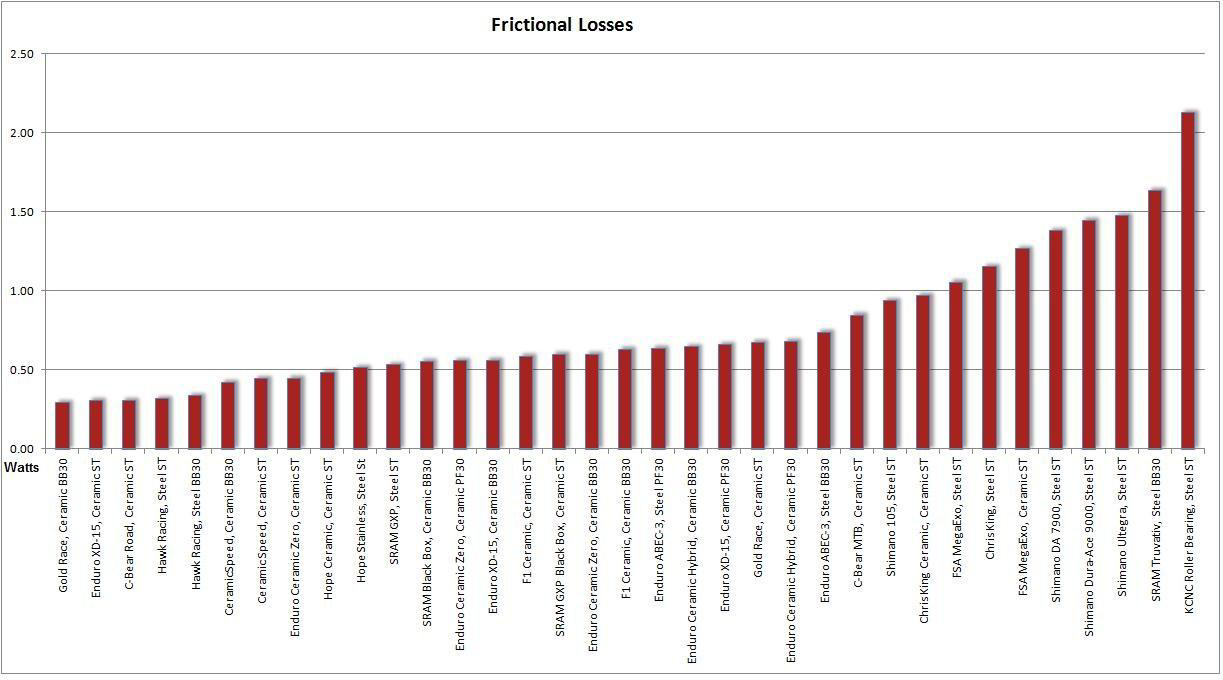
BBの比較と平均摩擦損失結果
上のグラフは、荷重をかけた状態での各サンプルの平均摩擦損失を示している。表示されている摩擦損失(ワット)は、3つの負荷試験条件の加重平均だ。BBには、ベアリングのモデル、ベアリングの材質、BBの規格が記されている。
負荷がかかった状態でのBBの摩擦抵抗は、0.29ワット(ゴールドレース、セラミックBB30)という低い値から、2.13ワット(KCNCローラーベアリング、スチールST)という高い値まである。
平均値は0.77ワット、中央値は0.63ワットだった。
平均摩擦損失に対する負荷比較
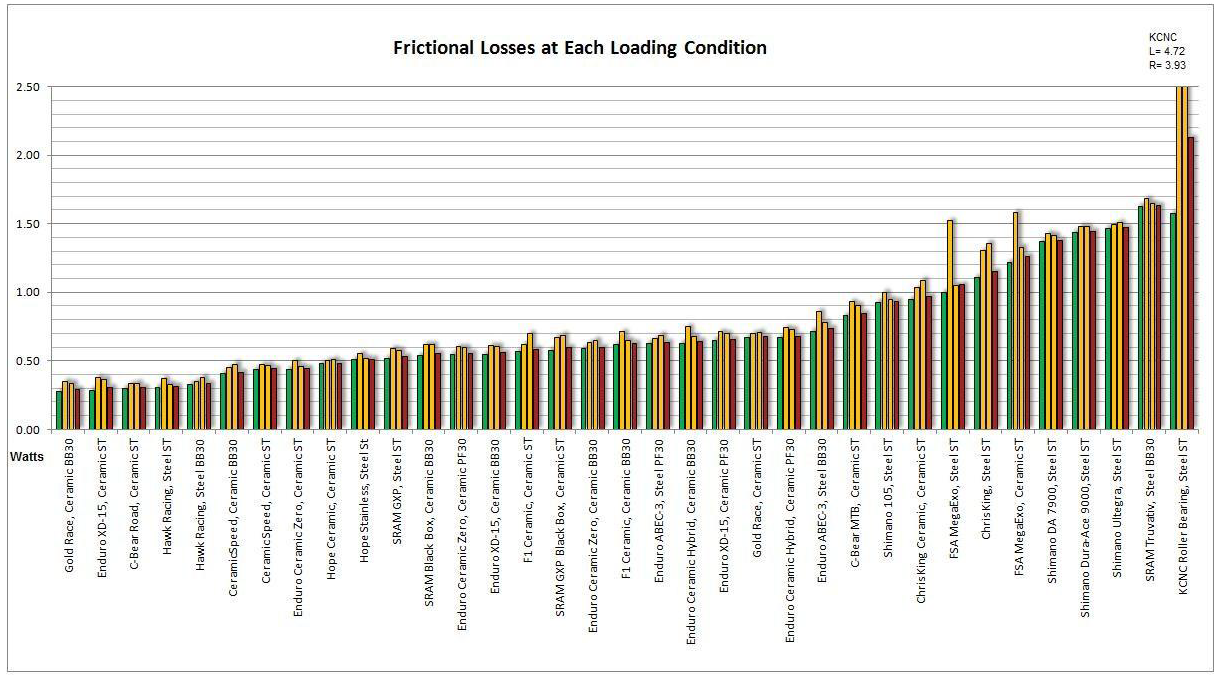
Frictional Losses at Each Loading Condition
加重平均を含む3つの荷重条件それぞれについて測定された摩擦損失は、上のグラフに示されている。
- グリーンのバーは、純粋な垂直方向荷重の測定値
- イエローのバーは、それぞれ左側と右側の垂直方向/横方向荷重の測定値
- レッドのバーは、加重平均
結論:
BB用途では、垂直方向深溝ベアリングとアンギュラコンタクトベアリングの両方が、3つの荷重条件のそれぞれで優れた性能を発揮する。どちらのタイプのベアリングも、荷重の種類によって不利になることはない。
ベアリング材料の比較:
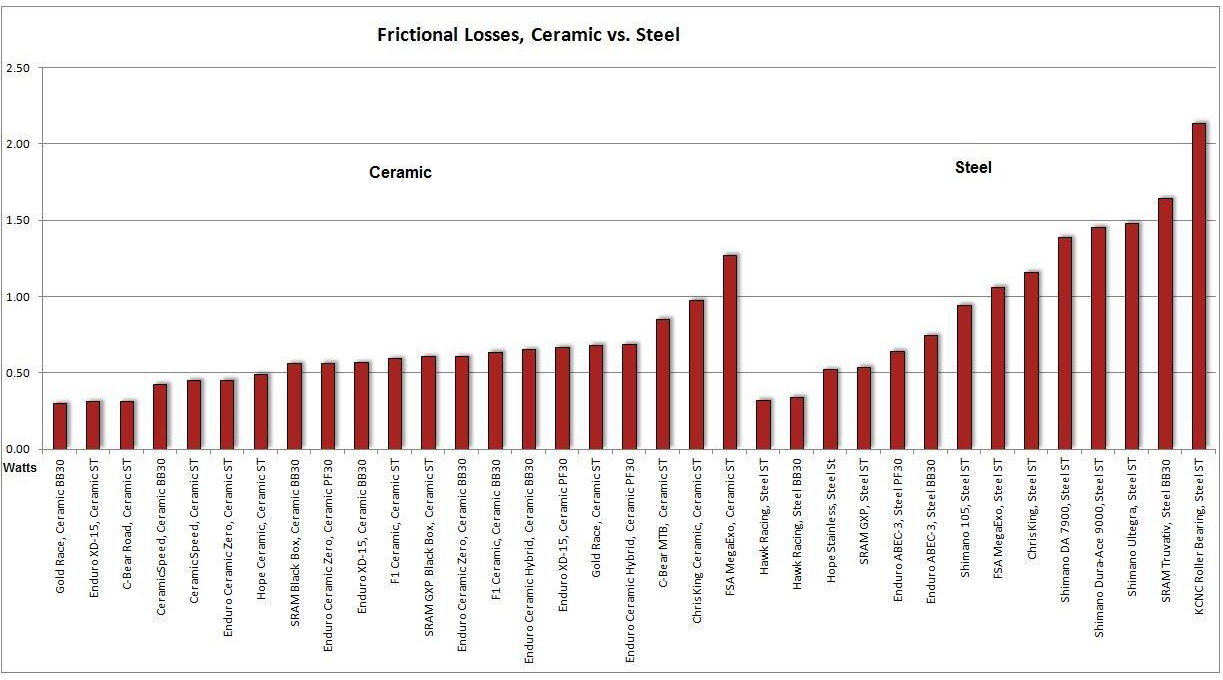
Frictional Losses, Ceramic vs. Steel
セラミック製とスチール製のさまざまなBBを選定し、この2つの素材の間に効率の違いがあるのかどうかを分析した。上のグラフは、平均的な摩擦損失をベアリング素材のタイプ別に分けたものである。
総合的な結果:
セラミック製BBの平均摩擦損失は0.60ワットで、スチール製BBの平均摩擦損失は1.02ワットである。
セラミックベアリングとスチールベアリングのこの違いは、「セラミックベアリングは一般的にスチールベアリングよりも摩擦が少ない」という、早合点してしまうが不正確な結論になりかねない。
テストした35個のサンプルのうち、多くは高価なセラミックである。他は低価格のスチール製だ。最高性能のセラミックと最高性能のスチールの摩擦損失を比較すると(ゴールド・レースは0.29ワット、ホーク・レーシングは0.32ワット)、その差は0.03ワットだった。
これは、ある種のスチール製BBが、最高のセラミック製BBと同等の効率(100分の3ワット以内)を発揮していることを示している。
したがって、ベアリングの材質だけから判断すると、セラミックベアリングは必ずしもスチールベアリングのBBよりも効率的とはいえない。ベアリングの効率は、素材そのものではなく、設計と使用する素材の品質に大きく左右される。
結論:
「セラミックはスチールよりも摩擦抵抗が小さい」という説は、必ずしも真実ではない。
最高性能のセラミックベアリングと最高性能のスチールベアリングの差は0.03ワットである。
セラミックとスチールの比較(メーカー内):
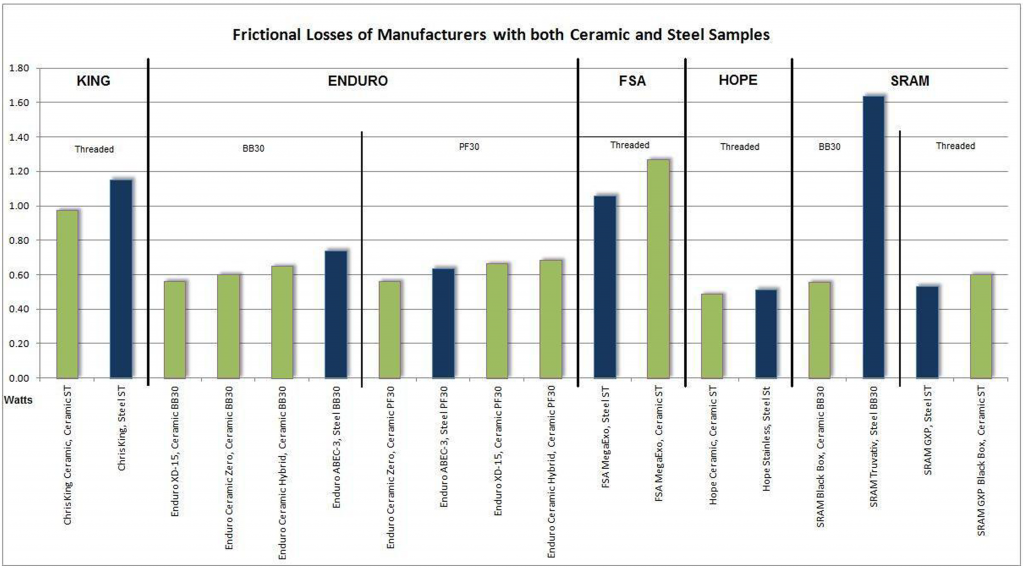
Frictional Losses of Manufacturers with both Ceramic and Steel Samples
セラミックとスチールの両モデルを同じ規格で比較した各メーカーの摩擦損失を検証した。
総合的な結果:
このテストでは、セラミック製とスチール製の両方のBBを持つ5つのメーカーのうち、3つのメーカーのセラミック製品が、同じ規格内でスチール製よりも高い摩擦損失を示した。通説とは異なる、「セラミック製品のほうが摩擦抵抗が大きい」結果だ。
結論:
ベアリングは、素材そのものだけでなく、デザイン(シェルや構造)の質、素材の質も考慮すべきである。
規格の比較:BB30と標準的なねじ切り(素材/メーカー同一):
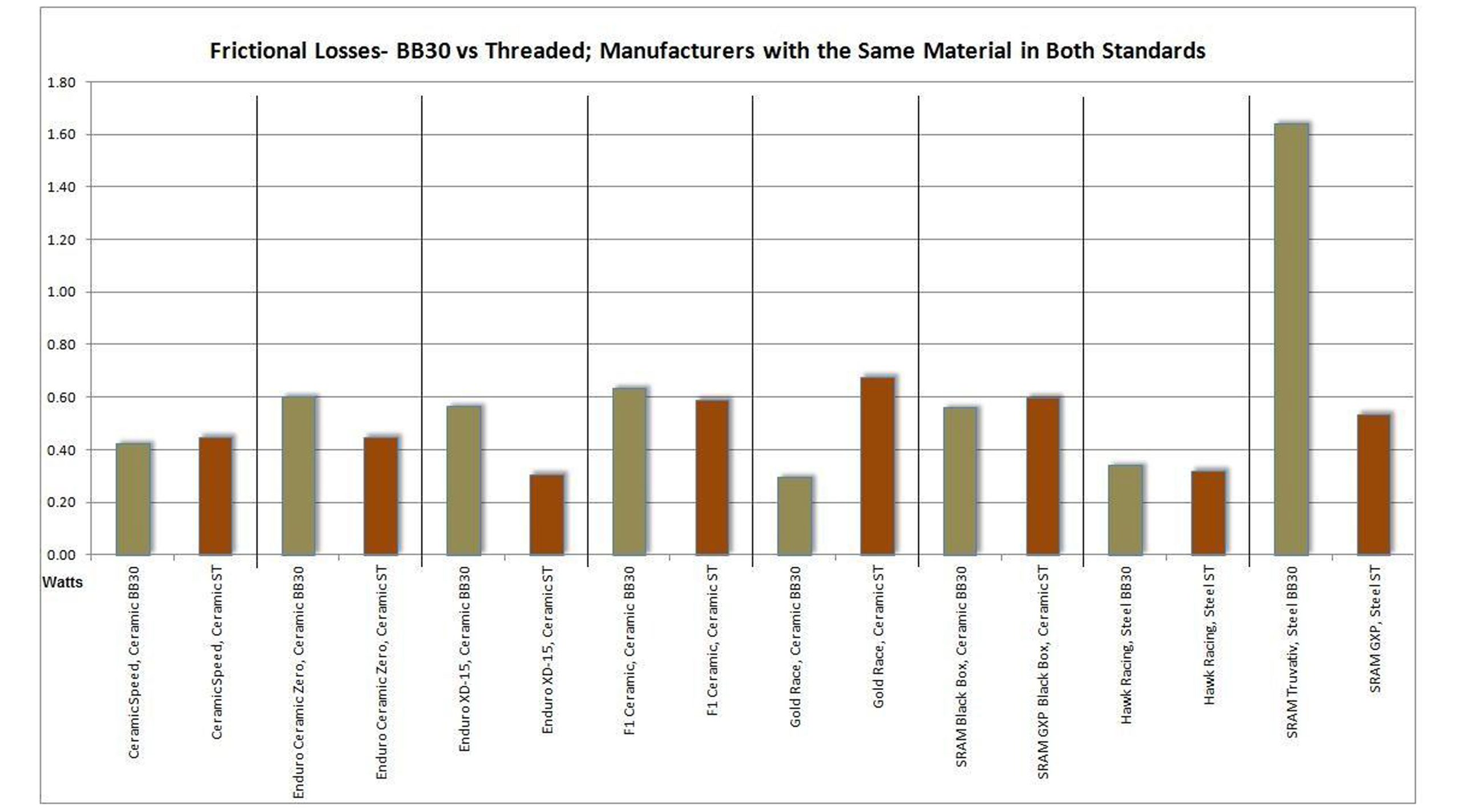
Frictional Losses- BB30 vs Threaded; Manufacturers with the Same Material in Both Standards
サンプルとして、同一メーカーの、同一素材で作られたBB30と標準ねじ切りのBBモデルが16サンプル(8セット)含まれている。
総合的な結果:
同一の負荷条件の下で、BB30と標準的なねじ切りBBの間に統計的に有意な差は存在しないことがわかった。
BB30と標準ねじ切りBBの摩擦損失の中央値は、それぞれ0.56ワットと0.049ワットであった。摩擦損失は、規格そのものよりも、BBのメーカー、品質、デザインに大きく左右される。
注意すべき点
スレッドBBのベアリングレース中心点から、ベアリングレース中心点までの幅(有効幅)は、BB30およびPF30スタンダードよりも大きい。
このBB幅の拡大は、クランクのスピンドルにかかる片持ちモーメントを減少させる。同じペダル踏力であれば、ベアリングにかかる垂直方向荷重を効果的に減少させることができる。
このテストでは、規格に関係なく、すべてのサンプルが同じような荷重条件でテストが行われた。これは、同じ荷重条件下で異なるBB設計を分析するために意図的に行われている。
これらを考慮し、結果に織り込んでいた場合、標準ねじ切りBBの摩擦損失の値は、およそ5~10%減少すると推定される。
結論:
同じ荷重をかけた場合、BB30規格やPF30規格に比べ、標準ねじ込みタイプのBBが優れている、あるいは劣っていることを示す傾向は存在しない。
BBの幅を考慮した場合、標準ねじ式の摩擦損失は、他のすべての条件が同じであれば、同等のBB30またはPF30よりも約5~10%低いと推定される。
無負荷状態でのBBの比較:
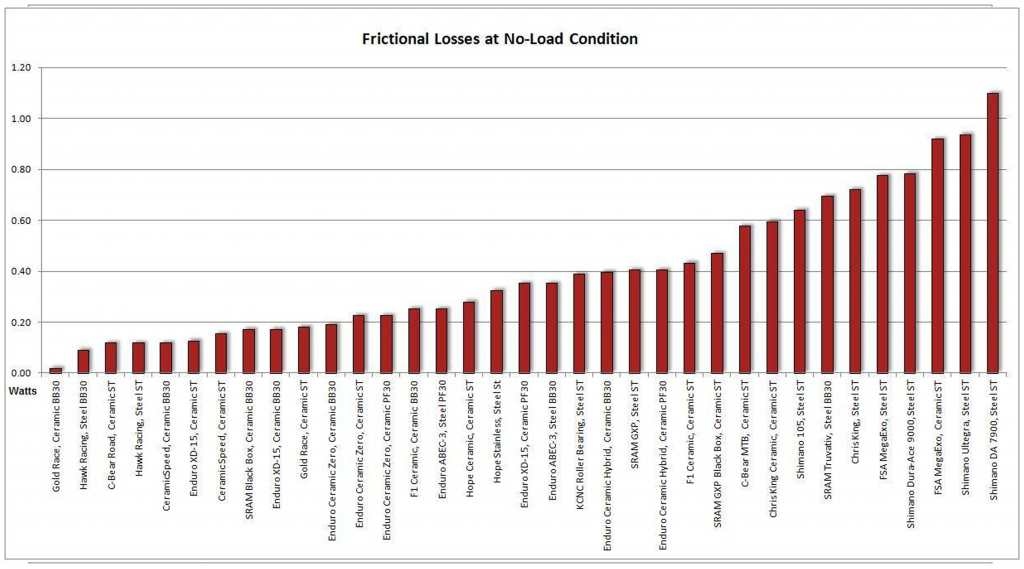
Frictional Losses at No-Load Condition
総摩擦損失に対するシールと潤滑の寄与を調べるため、荷重を取り除いた状態でサンプルを試験した。
なぜこのテストなのか?
このテストは、各BB内の摩擦損失の構成要素をよりよく理解するために行われた。 BBによって生じる摩擦の大部分は、3つの独自の要素に起因する。これら3つの独自要素はそれぞれ、BB全体の摩擦のかなりの部分を占める可能性がある。
- ボールベアリングがレース内を転がり(荷重を受け)、ボールとレースの相互作用の接触部内でわずかに変形し、摺動することによって生じる摩擦抵抗
- 潤滑油によって生じる粘性抵抗
- シールがレース(BB設計の場合は回転するベアリングカバー)と摺動することによって生じる摩擦抵抗
総合的な結果:
平均無負荷摩擦は0.40ワットで、中央値は0.32ワットだった。
無負荷時の摩擦は、そのほとんどがシールと潤滑油(粘性抵抗)によって生じている。ボールとレースの相互作用は、シールと潤滑油によって生じる摩擦に比べ、無負荷状態では最小限の摩擦しか生じない。
無負荷はベアリング素材(セラミックやスチール)そのものの抵抗を示しているのではなく、シールと潤滑油の摩擦の結果を表している。
平均無負荷摩擦(0.40ワット)と平均負荷摩擦(0.77ワット)を比較すると、総摩擦の大部分は、実際のボール/レース摩擦(48%)よりも潤滑油とシール(52%)によって生じていることがわかる。
※[総負荷摩擦]=[無負荷摩擦(シールと潤滑油による寄与)]+[負荷摩擦(ボールとレースの相互作用による寄与)]という計算を用いた。
この計算は、ボールとレースの相互作用によって生じる摩擦損失が「荷重に大きく依存する」のに対して、シールと潤滑油によって生じる摩擦損失は「荷重に完全に依存しない」という仮定に基づいて行われている。
理論的に言えば、無負荷のBBの摩擦を測定し、総負荷摩擦から差し引くと、結果として得られる値は、負荷がかかった状態でボールとレースの相互作用によって生じる摩擦になる。
総負荷摩擦 – 無負荷の摩擦 = 負荷がかかった状態でボールとレースの相互作用によって生じる摩擦
現実的には、この摩擦損失の分別方法は絶対的なものではない。しかし、摩擦を発生させる各成分の貢献度を示す一般的な指標になる。
重要な注意事項
このテストは、BBの効率のみを評価するものである。長寿命や耐久性に影響するシールや純正潤滑油の設計など、その他の重要な特徴は考慮されていない。
粘度の高いグリースは長寿命であるが、一方で粘性抵抗が大きくなる。逆に、粘度の軽いオイルは粘性抵抗を最小限に抑えるが、ベアリングの寿命とメンテナンス間隔の頻度を犠牲にする可能性がある。
ベアリングの設計者は、製品の使用目的に基づき、風雨や異物からの保護を最大化することと、高効率のためにシール抵抗を最小化すること、それぞれのバランスを達成する必要がある。目標は、用途に応じた耐久性を持ちながら、効率的なBBを実現することにある。
ゴールドレース社のBB30ボトムブラケットは、最大効率を達成するためにとられた設計手法の一例である。
ゴールドレースのベアリングは最大限の効率を高めるためにシールの内径が実際のベアリング内径よりも小さく設計されている。かつ、非接触シールでグリスではなくオイルの使用をしている。
シール内径は実際にはインナーレースに接触していない。隙間が見える。この隙間(と、それに続く非接触シールによる摩擦)が、ゴールドレースが(グリースではなく軽油の使用とともに)最も低い無負荷摩擦損失を示す理由と思われる。
しかし、この設計は、汚れた状態で使用した場合、ベアリングに汚染物質が入りやすい。実際、ゴールドレース社の説明書には、「サーキットやクリーンなロードレースでの使用のみを推奨」としている。
シールと潤滑剤の効果を示すもうひとつの例は、C-Bear製品に見ることができる。
C-Bear社によると、ロード用BBとMTB用BBの内部ベアリングは同一である。しかし、MTB用にはより頑丈なシールとより重量のあるグリースが組み込まれ、過酷な条件下でも長寿命と耐久性を発揮する。そのため、MTBバージョンの摩擦損失はロードバージョンより0.54ワット大きい。
このテストでは、規格に関係なく、すべてのサンプルが同じような荷重条件でテストされた。 これは、同じ荷重条件下で異なるBB設計を分析するために意図的に行われている。
結論:
摩擦損失には、シール、潤滑油、ボールとレースの相互作用がそれぞれ関与している。計算上、全サンプルの平均を見ると、シールと潤滑油の摩擦の寄与は、ボールとレースの相互作用のそれよりもわずかに大きい。
シール設計と工場出荷時の潤滑剤は、使用目的や耐久性、寿命、性能の必要性によって大きく異なる。ボトムブラケットを選ぶ際には、使用目的、メンテナンス要件、特定のボトムブラケットの構造を考慮し、特定のサイクリング用途に適合することを確認することが重要である。
試験方法とデータ
実際の実験方法、摩擦抵抗の測定方法、試験装置について。
BB効率試験装置
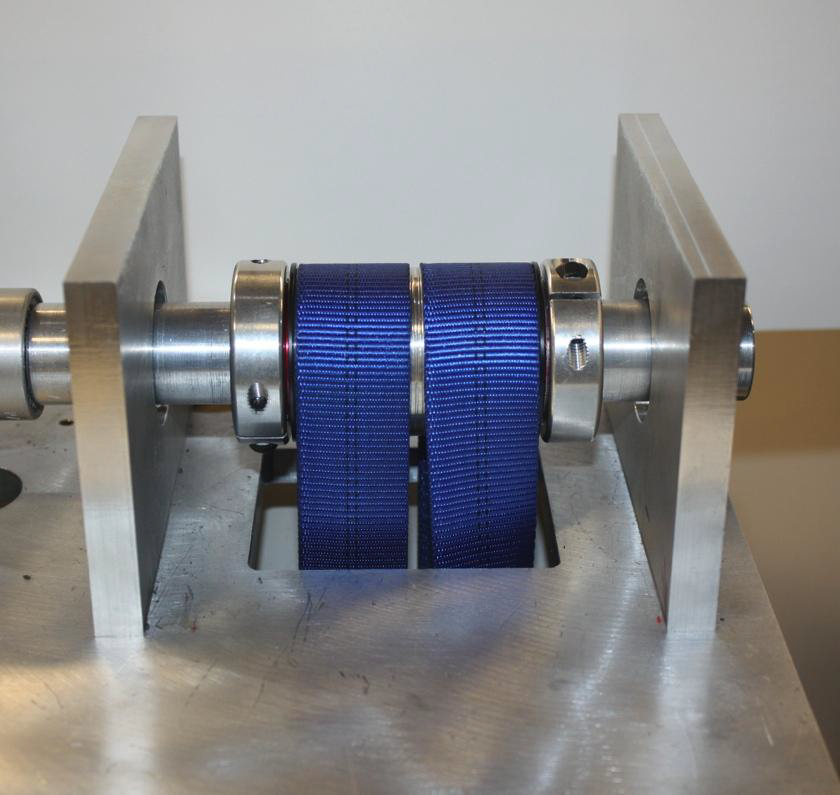
サポートプレート、治具用ベアリング、シェル内のBB、BBの位置決めクランプ、ローディングストラップを示す側面。 この写真はPF30シェルと、ストラップの外縁に隣接するPF30ボトムブラケット・ハウジングのリップ(黒いプラスチック)を示している。 (治具用ベアリングの位置決めクランプはこの写真には写っていない)。
BBの効率をテストするために、比較的シンプルな設計を採用した。
この設計は、シャフトを支える治具用セラミックベアリングとBB用ベアリングのセットで構成されている。この治具用ベアリングがシェルに取り付けられたBBを支え、シェルに荷重がかかるようになっている。
シャフトが回転すると、BBのベアリングと治具用ベアリングを含むシステムの総摩擦が測定される。治具用ベアリングの損失(機器の損失)は測定から除外される。その結果、テスト中のBB単体の摩擦損失値を得ることができる。
BBを取り付けたシェルは、業界標準のBB30、プレスフィット30(PF30)、標準的なねじ切りBBシェルである。 これらのシェルは、フレームメーカーがフレーム製造に使用するBBシェルと同じもので、メーカーから調達している。
左右のベアリングに均等に荷重がかかるように、シェルの上部に幅の広いナイロン製のストラップを通して荷重をかけた。 外径(OD)がBBの内径(ID)に一致するシャフトをBB(クランクスピンドルとして機能)に挿入している。
シャフト、BB、荷重用ストラップは、2つのセラミック製固定具ベアリングによって支持されている。シャフトに対してBBを固定し、BBに軽い予荷重を与えるためにクランプが使用された。 もう1組のクランプは、シャフトを治具用ベアリングに横方向に固定するために、治具用ベアリングの外側で使用された。
これらのクランプは、横方向の荷重条件下でシャフトとBBが水平方向にスライドしないようにした。
シェル(BBが内部に取り付けられている)、ストラップ、荷重は、シャフトが95RPMでシェル内部を回転する間、静止したままである。駆動モーターとシャフトの間にインラインで設置された回転トルクセンサーは、BB内の2つのベアリングと2つの治具用ベアリングによって生じる総摩擦(トルクとして)を測定する。
精度と一貫性を維持するため、試験全体を通して同じ治具ベアリングを使用している。異なる外径のシャフトを、異なる内径のBB規格に適合させる必要があったため、外径の異なるシャフトが固定内径を持つ同じ治具ベアリングに適合できるよう、異なるサイズのシャフトごとにアダプターを製作している。
治具用ベアリングの摩擦損失(垂直方向荷重条件と横荷重条件の両方)は、テスト前のキャリブレーションで既知の量である。治具用ベアリングの摩擦損失は、測定された摩擦損失の合計から差し引かれ、その結果、被試験ボトムブラケットの摩擦損失が得られる。
測定器の精度は±0.01ワットである。
全手順
- BBをそれぞれのシェル(BB30、PF30、標準ねじ切り)に取り付け、装置に設置した。
- クランク調整ナットを指で締めた状態をシミュレートするため、アウトボードクランプを介してBBに軽いプリロードをかけた。慣らし運転とテストはすべて95RPMで行った。
- 各BBに52キログラムの垂直方向荷重をかけ、1時間かけて慣らしを行った。この時間の目的は、ベアリングの潤滑油とシールを慣らすことである。
- 慣らし運転後、右側に9キログラムの横荷重をかけ(慣らし運転でBBにかけた52キログラムの垂直方向荷重に加えて)、3分後に計測を記録した。9キログラムの横荷重を右側から取り除き、左側に加え、3分後に2回目の計測を記録した。これが「右横」と「左横」の測定値である。
- 機器の平均化は15秒に設定された。つまり、すべての測定値は15秒間のデータの平均値である。
- 左横方向の測定が記録された後、横方向の荷重が取り除かれ、純粋な52キログラムの垂直方向荷重のみが残された。そして3分後に測定値が記録された。これが “純粋な垂直方向 “の測定である。その後、垂直方向荷重を取り除き、フリースピンを防ぐためにBBを固定した。これでBBは無負荷となった。この測定は「無負荷」測定である。
- 4つの負荷条件それぞれについて、装置固定用ベアリングの摩擦損失(装置損失)は、装置の初期設定と校正の際に決定された。これらの機器損失は未加工の測定値から取り除かれた。従って、記載されている結果データは、テスト中のBBサンプルの摩擦損失のみである。
荷重計算
ボトムブラケットのベアリングは、一般的なライディングで様々な負荷にさらされる。ライダーの全体重がペダルにかかり、チェーンがフロントアウターチェーンリングに入っている場合、リアに小さなギアを使うとチェーンの張力が大きくなる。この場合、チェーンの張力が大きくなり、BBにかかる反力も大きくなる。
このテスト(純粋な垂直方向荷重条件)でかかった荷重は52キログラムだ。この荷重は、ライダー出力250ワットでの定常走行中にBBが受けるおおよその平均荷重である。この計算の前提は以下の通り。
- クランク長:175mm
- チェーンリング:53T
- ケイデンス:95rpm
- 定常出力:250W
この計算では、ライダーのペダル踏力による負荷、ペダリングのダウンストローク中のピーク負荷、張ったチェーンによる反力、さらに片持ち効果(ペダルとチェーンリングの負荷点がベアリングのそれぞれの中心線より外側にあり、モーメントが生じる)を考慮している。
ドライブ側のベアリングと非ドライブ側のベアリングは、ペダルストロークのどのポイントでも異なる荷重を受ける。ドライブ側のベアリングは、チェーンリングの反力がドライブ側にあるため、非ドライブ側のベアリングよりも平均荷重が大きくなる。
この試験で使用した52キログラムは、両方のベアリングに均等にかかった荷重の合計平均値である。 横方向の荷重条件は、ベアリングの両側に9キログラムを加え、垂直からずれた荷重条件をシミュレートした。
この横荷重は、ライダーがサドルの外でペダルを漕いでいるときの姿勢に近い、垂直から10°ずれた姿勢になることを想定している。
ベアリングを構成する要素の摩擦抵抗割合
大手のメーカーには、エンドユーザーの技術的なアドバイスに回答するエンジニアリング部門が設けられている。SKF、NTN、NSK、シェフラー(FAG / INA)は、ベアリングの部品(シール、グリス、転がり抵抗)別の摩擦損失の割合を示す資料をエンドユーザー向けに開示しいる(下図参照)。
ベアリングの各コンポーネントに関連する摩擦の割合はわずかに異なるが、全体的な値と順序は基本的に同じだ。ベアリングの総摩擦抵抗のうち、ベアリングシールが最大の摩擦損失である。潤滑剤がそれに続く抵抗であり、転がりの摩擦損失は非常に小さいことがわかる。
さらにシェフラー(FAG / INA)は、もう1歩踏み込んだベアリングの構成要素別の内訳も示している。
シェフラーのデータが貴重かつ重要である理由として、スチールからセラミックベアリングに変更した場合の有効性と事実を把握するために役立つ。素材をスチールからセラミックに変更したとしても、摩擦抵抗を改善できる割合は最大3%程度しか期待できない。
実際には、転がりの摩擦をなくすことはできないため、3%のうち10%、すなわち0.3%ほどしか摩擦抵抗の削減を見込めない。
セラミックベアリングは、ほとんどの場合リテーナー内にスナップがあるため、リテーナーの摩擦に注意する必要がある。これらは、金属リテーナーよりも摩擦が大きいことが一貫して示されている。
したがって、セラミックベアリングは転がり摩擦を減らすことが可能である(3%)が、リテーナーの摩擦は必然的に増加する(7%)。
最終結果としてセラミックベアリングを使用したからと言って摩擦抵抗が小さくなるとは限らない。むしろ、条件しだいではスチールベアリングのほうが摩擦が小さくなる可能性がある。
これらの事実を実際に確認するために、グリスとシールの効果を試す実験は以下だ。Enduro製のセラミックベアリングとNTN LLB(非接触)スチールベアリングの2つのベアリングを、分解しさまざまな条件の違いで摩擦損失を測定した。
下のグラフは右に行くに従い異なるプロセスを示している。
ベアリングは3つの異なる状態に変更しながら測定を実施している。はじめは箱から出したあと、すぐに使用する。2番目はグリスの除去を行いオイルを注油した。3番目はグリスの除去、シールの除去、そしてオイルの交換を実施した。
箱から出した状態において、Enduroベアリングの電力損失はわずかに低くなる。グリスが除去されると、両方のベアリングの電力損失はほぼ等しくなる。 シールを取り外したあと、NTNベアリングの摩擦が優位になる。
これは、NTN、NSK、SKF、およびシェフラーなど世界三大ベアリングメーカが提供するデータと相関関係にある。
まとめ:
セラミックベアリングはスチールベアリングよりも摩擦抵抗が小さい、という一般的な通説は必ずしも真実ではない。
最高性能のセラミックベアリングと、最高性能のスチールベアリングの摩擦損失の差は、0.03ワットだ。3つのメーカーのスチール製ベアリングは、セラミック製ベアリングよりも摩擦抵抗が小さかった。
ベアリングの効率は、設計、素材の質、負荷の方向に基づいている。必ずしも「素材の種類(セラミックやスチールなど)」によって決定するわけではない。
総摩擦損失に寄与する個々の部品を分析すると、「シール」と「潤滑油」による摩擦損失は、ベアリング自体による摩擦損失(ボールとレースの相互作用摩擦)よりも大きい。
つまり、摩擦損失は「シール・潤滑油ロス > ボールとレースの相互作用摩擦」の関係が成り立つ。
また、同一のベアリングを用いた場合でも、BBの規格(構造や方式)が異なると摩擦抵抗が異なり、変化する。フレームを選ぶ際は、BSA、ITA、T47などスレッド方式が望ましい。
最も摩擦抵抗が大きいKCNCローラーベアリングスチールは2.13ワットの損失がある。ベアリング抵抗を限りなくゼロに近づけたとしても、期待できる改善は2ワット弱である。この値に対して、費用対効果を考慮し、ベアリングの選定では合理的な決断を下す必要がある。
セラミックベアリングはスチールベアリングよりも摩擦抵抗が小さい、というのは真実ではない。
プロモーション目的や、無負荷の空転だけでベアリング性能の善し悪しを表現する(大部分がシールと潤滑油の摩擦を表している)ような、性能観点のすり替え、子供だましの戦略に対しては、本質的に何の性能を示しているのか、どのような負荷条件なのか、総合的に見定め、鵜呑みにせず判断していく必要がある。
セラミックベアリングの性能を信じる人、懐疑的な人、全ての人に今回の実験内容が伝われば幸いだ。